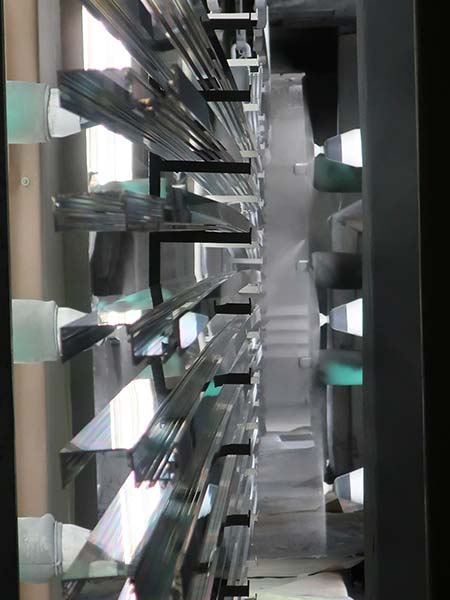
Coil-Coat & Spray Application
A consistently random flake orientation is the ideal medium. Achieving this is practical and realistic with “coil-coated” sheet stock. With a coil coating process, there are virtually no application variables involved. Part geometry – continuous flat sheet – is constant, spray distance is constant, etc. As a result, it is possible to attain a consistent random orientation of the metallic flakes, and a uniform color and brightness.
Unfortunately, a spray-application process has more variability which reduce the ability to achieve perfectly random flake orientation. These process variables include different part geometries, electrostatic/grounding effects (even if electrostatic equipment is not used), fluid pressures, paint to part distances, overlapping spray areas, and supplemental handspray to reach recessed or corner areas.
As a result, spray-application – which will be used on any aluminum parts other than flat sheet in stock colors – will often show some variation on metallic paints. Faced with this reality, the question for architects, owners, contractors and material suppliers then becomes how to manage and minimize the risk of metallic variation.